Interco Recycles Foundries & Die Casters
As one of the largest indoor, nonferrous metal recycling facilities in North America, Interco works closely with the metal casting industry including foundries and die casters. Interco contributes to the vast world of manufacturing recycling by recycling metal scrap, including aluminum, zinc, brass, and bronze. Interco’s experience and extensive partnerships allow them to maximize the return on investment when recycling nonferrous metals. Foundries and die casters around the world rely on Interco for scrap metal recycling.
The Interco Facility is Equipped to Recycle Metal Scrap on a Large-Scale
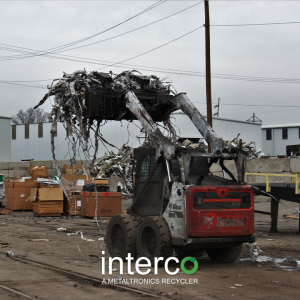
Interco recycles foundries and die casters scrap at their the 450,000+ square foot recycling facility. The Interco recycling facility is comprised of seven buildings on more than 45 acres centrally located on the Illinois-side of St. Louis in the shadows of the Gateway Arch. The Interco recycling facility processes over 20 million pounds of material per month. The facility boasts a 145,000 square foot processing plant dedicated to the processing of computers and electronics. The remainder of the indoor facility is used to recycle nonferrous metals.
Some aspects of scrap metal recycling can be dangerous. The staff at Interco is highly qualified to safely recycle high-risk materials. Several certifications demonstrate the company’s commitment to safe and secure recycling practices:
- R2v3 – Responsible Recycling Standards
- ISO 14001 – Environmental Management Systems
- ISO 9001 – Quality Management Systems
- ISO 45001 – Occupational Health and Safety Assessment Series Management Systems
Interco Recycles Nonferrous Metals
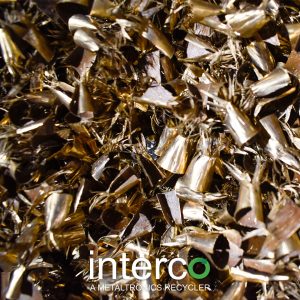
Interco processes over 12 million pounds of nonferrous material each month. The company uses several different processes to recycle nonferrous metals:
- Firstly, both mechanical separators and hand sorting techniques separate metals according to grade.
- Secondly, if necessary, the materials undergo processing in the metallic powder and dust separation plant.
- Next, a machine shreds the the sorted metals into smaller pieces.
- Lastly, the sorted, graded, and processed metals are packaged for shipment to end customers. These customers will refine and smelt the metal into ingots for manufacturers to use to make new products.
Foundries and die casters scrap contributes to both sides of the recycling process. The metal casting processes produces slag, dusts, dross, and off-spec alloys. Nonferrous metals such as, aluminum, copper, lead, nickel, brass, bronze, and zinc make up the majority of these metals. Interco buys these items containing nonferrous metals and processes them into smelter-ready materials. On the other hand, many foundries and die casters use the recycled metal scrap to metal cast new goods.
Maximizing ROI for Foundries and Die Casters Scrap
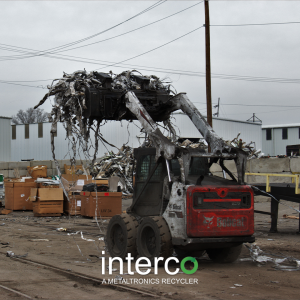
Unlike many recyclers, Interco has many years of experience in mixed load recycling of nonferrous metals and electronic scrap. The company receives approximately 50 mixed loads each day equaling one load every nine minutes. Additionally, Interco understands that many suppliers are unable to obtain the necessary inbound load minimum required by smelters, refineries, and manufacturers. When a supplier recycles metal scrap with Interco, a mixed load can contain five to ten different items. Items could include slag, fume collector dusts, dross, and off-specification parts, among others.
The Interco commercial department has established contracts with smelters, refineries, manufacturers, and mills across the world. Interco sorts, grades, and processes materials into smelter-ready metals, therefore, the need for a middleman or broker is eliminated. As a result, smelters and refineries rely on Interco as a supplier to provide a recurring stream of material. Additionally, the contracts with these companies allow Interco to pay top dollar to their sellers. Therefore, the company is typically able to buy at higher prices than other recyclers who must search for an end consumer.
The Importance of Scrap Metal Recycling
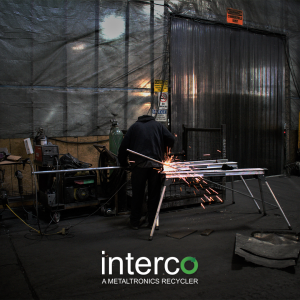
Foundries and die casters are some of the largest contributors to the manufacturing recycling movement. They melt and recast millions of tons of scrap metal every year to create new goods. Foundries and die casters rely on metal recycling for a sustainable source of material. Manufacturers use 15-20 million tons of scrap metal each year in the remake of new metal casting. Otherwise, these scrap metals would go to landfills. Consequently, without recycling, the price of die casting would increase by 20-40%.
Making castings from recycled metals also saves energy and conserves natural resources. Compared to the process of raw materials, castings made from recycled metals use 95% less energy to make. Through recycling, materials do not enter the waste stream. The reduction of recyclable metals entering the waste stream lowers the impact of potentially toxic materials entering the environment. Therefore, the overall strain on landfills and the environment is reduced.
Choose Interco to Recycle Foundries and Die Casters Scrap
Interco specializes in the placement of smelter-ready materials catering to a broad array of industrial, dealer, and government organizations. The company ships nonferrous scrap worldwide utilizing established partnerships with end consumers in the United States, Europe, Latin America, and Asia. As a result, foundries and die casters all over the world rely on Interco to recycle metal scrap.
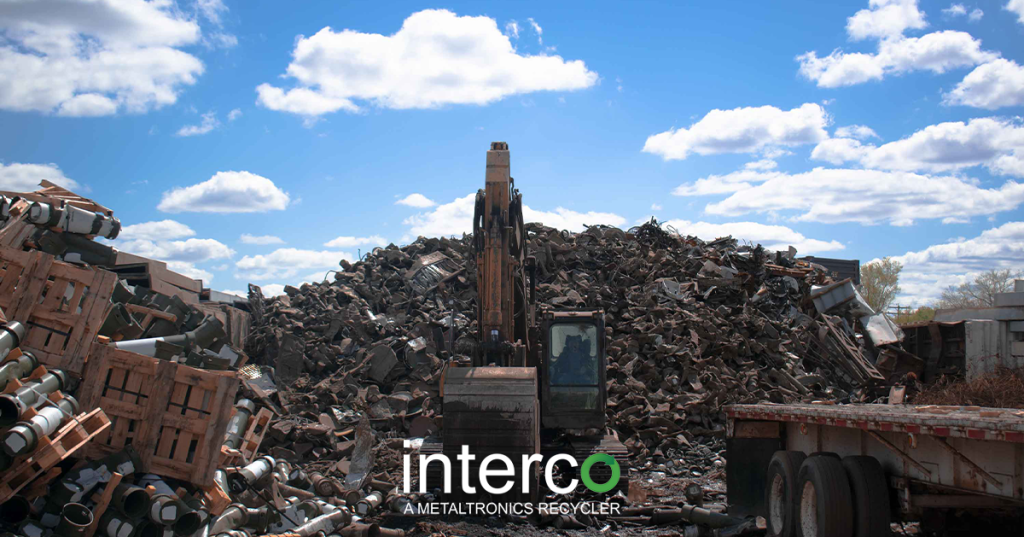